Understand the crucial difference between NO3-N and NO3- in forage testing. Are your cattle safe? Learn how to interpret lab results to ensure their health.
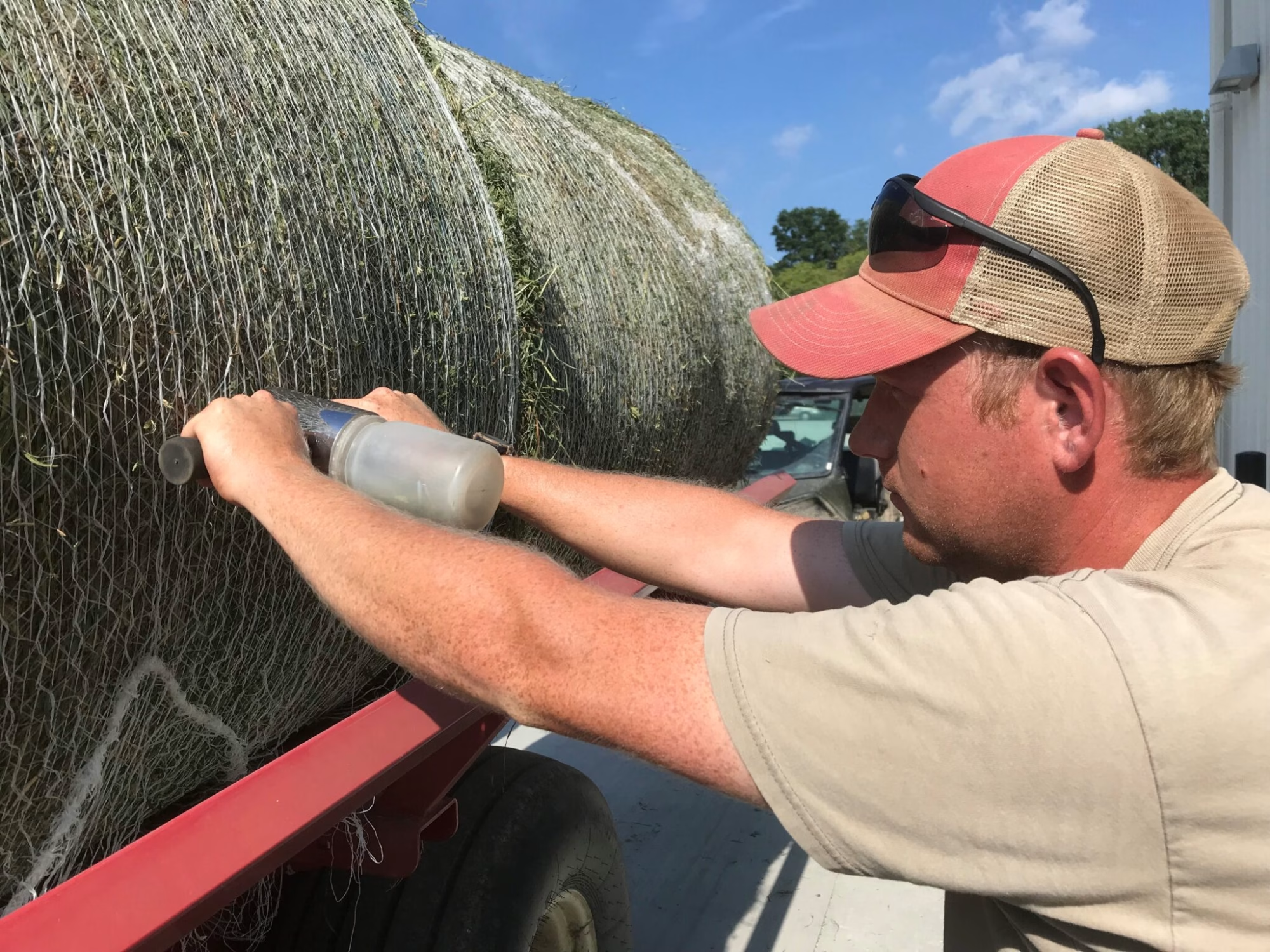
Imagine the potential risk of losing part of your cattle herd due to the forage they consume. This risk underscores the importance of monitoring nitrate levels in forage, as high levels can lead to fatal poisoning. Therefore, distinguishing between NO3- (Nitrate) and NO3-N (nitrate-nitrogen) is crucial and a matter of life and death for your herd. Misinterpreting these readings can be the difference between safe consumption and dangerous toxicity levels. Understanding these distinctions is critical for making informed decisions that protect your herd’s health. Nitrogen comprises only 22.6% of the nitrate ion, highlighting the importance of accurately reading forage test results. Labs may report these values differently, and without a clear understanding, producers might underestimate or overestimate the danger. This topic is vital as it safeguards cattle producers’ livelihoods and their animals’ well-being.
Deciphering the Difference: Nitrate vs. Nitrate Nitrogen
Nitrate (NO3-) comprises one nitrogen atom and three oxygen atoms, making Nitrogen about 22.6% of the nitrate ion. Conversely, nitrate nitrogen (NO3-N) represents just the nitrogen part of this compound. This distinction is crucial for interpreting test results accurately and assessing forage toxicity. Understanding these differences ensures precise evaluations of forage safety.
The Critical Difference in Nitrate Reporting Methods
When laboratories report nitrate levels, they use one of two methods, yielding different results. Some labs measure the nitrate ion concentration (NO3-), including Nitrogen and oxygen. Others focus on the Nitrogen within the nitrate ion, reporting it as nitrate-nitrogen (NO3-N). The distinction is crucial because Nitrogen is only 22.6% of the nitrate ion. A test showing 3,000 parts per million (ppm) of NO3- suggests much lower toxicity than the same result for NO3-N, indicating a higher nitrate concentration. To accurately assess forage safety, always check if nitrate levels are reported as NO3- or NO3-N. Understanding the reporting method ensures that discussions about forage safety and nutrition are based on comparable data. Mathematical conversions can help, but initial clarity on the reporting method is essential.
Toxicity Thresholds: Understanding and Distinguishing Critical Safety Levels
Toxicity Thresholds: Nitrate (NO3-) levels become concerning at 9,000-10,000 ppm, while nitrate nitrogen (NO3-N) poses a danger at 2,000-2,300 ppm. Recognizing these thresholds is crucial for ensuring forage safety and livestock health.
Forage toxicity can severely impact livestock well-being and productivity. Elevated nitrate levels disrupt oxygen transport, potentially leading to conditions like methemoglobinemia. This is not just a matter of safety but also of empathy and care for your animals. Accurate concentration knowledge is vital for necessary precautions. Various reporting methods in forage test reports often need to be clarified. Still, proper interpretation helps avoid toxicity risks and keeps livestock feed safe. Utilizing the correct thresholds protects animal health and supports sustainable farming.
Excess forage nitrates can also indicate environmental issues, such as nutrient runoff, that affect water bodies. Thus, understanding nitrate toxicity is crucial for both agriculture and ecological conservation.
Mastering Nitrate Conversion Formulas: A Vital Tool for Forage Safety
Understanding and applying these conversion formulas is essential for accurately interpreting forage test results and determining the safety of your feed. Nitrate = nitrate nitrogen x 4.43 and Nitrate Nitrogen = Nitrate x 0.226 allow you to convert measurements between these two forms.
To illustrate, let’s use an example. Suppose your forage test results show a nitrate nitrogen level of 3000 ppm. To find the equivalent nitrate level, you would multiply this value by 4.43:
Nitrate = 3000 ppm (NO3-N) x 4.43 = 13,290 ppm (NO3-)
Conversely, suppose your report indicates a nitrate level of 3000 ppm. In that case, you can convert this to nitrate Nitrogen by multiplying the nitrate value by 0.226:
Nitrate Nitrogen = 3000 ppm (NO3-) x 0.226 = 678 ppm (NO3-N)
By employing these formulas, producers, and nutritionists can ensure they interpret results correctly and make informed decisions about the safety of their forage.
A Practical Scenario: Unveiling the Critical Safety Implications of a 3,000 ppm Nitrate Score
Consider a practical scenario where a forage test result shows a nitrate score of 3,000 ppm. As a producer, it’s crucial to identify whether this score is reported as nitrates or nitrate nitrogen, as this distinction will determine the safety of the forage for your livestock.
The situation becomes hazardous if the 3,000 ppm result is reported as nitrate-nitrogen (NO3-N). The danger level for NO3-N ranges between 2,000-2,300 ppm, so a result of 3,000 ppm indicates a high concentration exceeding the safe threshold by 700-1,000 ppm. This level is almost 50% higher than what is considered toxic, and feeding this forage without proper management could lead to nitrate toxicity, posing severe health risks.
Conversely, if the 3,000 ppm result is reported as Nitrate (NO3-), there’s no immediate cause for concern. The critical safety level for nitrates begins at around 9,000-10,000 ppm. Therefore, a forage test result of 3,000 ppm nitrate is well below the danger threshold, representing less than one-third of the hazardous level. Under this designation, the forage is considered safe for livestock consumption without special precautions.
This example underscores the importance of distinguishing between nitrate nitrogen and nitrates. By correctly interpreting forage test results, producers can ensure the health and safety of their livestock. This responsibility is not to be taken lightly. Always verify the reporting method used by your lab and use the conversion formulas to understand the nitrate levels in your forage. Your commitment to this process is crucial for the well-being of your animals.
Interpreting Forage Test Results Accurately: Essential Tips for Producers and Nutritionists
Interpreting forage test results accurately is crucial for ensuring the safety and quality of your feed. Here are some practical tips for producers and nutritionists:
- Identify the Metric Used: Read the forage test report carefully to determine whether the nitrate levels are reported as Nitrate (NO3-) or nitrate nitrogen (NO3-N). This distinction is fundamental to understanding the results correctly.
- Consistent Communication: When discussing nitrate levels with others, such as advisors or fellow producers, always specify the referenced metric. Miscommunication can lead to incorrect interpretations of feed safety.
- Nitrate = Nitrate Nitrogen × 4.43
- Nitrate Nitrogen = Nitrate × 0.226
- Utilize Conversion Formulas: Familiarize yourself with the conversion formulas to translate between nitrate and nitrate nitrogen if necessary. Use the formulas:
- Double-check thresholds: Compare the reported values against established safety thresholds. For nitrates (NO3-), the danger level starts at 9,000-10,000 ppm, while for nitrate nitrogen (NO3-N), it is between 2,000-2,300 ppm.
- Keep Records: Maintain thorough records of all forage test results, specifying the metric used for each test. This documentation will facilitate accurate comparison over time and ensure consistent safety assessments. Consult Expertise: When in doubt, consult with forage specialists or extension services for an expert opinion on interpreting the results and making informed decisions about feed safety.
By following these practical guidelines, producers and nutritionists can ensure they accurately interpret forage test results and maintain clear, consistent communication about nitrate levels. This approach will help safeguard livestock health and optimize forage utilization.
The Bottom Line
The distinction between Nitrate (NO3-) and nitrate nitrogen (NO3-N) is not just an academic nuance; it is crucial for cattle feed safety. Different lab reporting methods can yield varying results, emphasizing the need to understand specific toxicity thresholds: 9,000-10,000 ppm for NO3- and 2,000-2,300 ppm for NO3-N. Accurate interpretation requires using the correct conversion formulas—Nitrate = Nitrate Nitrogen x 4.43 and Nitrate Nitrogen = Nitrate x 0.226. Ensure you know how your forage results are reported to make informed, consistent decisions about feed safety. Scrutinize your lab reports and employ appropriate conversions to safeguard your livestock’s health. Vigilance in examining and interpreting nitrate data is not just a task but a responsibility. Protect your cattle from nitrate toxicity by understanding the nuances of forage test results. Your diligence can make all the difference.
Key Takeaways:
- Forage test results can report nitrates in two ways: as nitrate (NO3-) or as nitrate nitrogen (NO3-N).
- Nitrate (NO3-) measures the concentration of the entire nitrate ion, while nitrate nitrogen (NO3-N) indicates the amount of nitrogen within the nitrate ion.
- Nitrate (NO3-) is only 22.6% nitrogen by weight.
- Danger levels differ significantly between these metrics: For NO3- it’s 9,000-10,000 ppm, and for NO3-N it’s 2,000-2,300 ppm.
- Both methods provide the same information but require careful attention to ensure consistency in interpretation and discussions.
- Conversion between nitrate and nitrate nitrogen is straightforward: NO3- = NO3-N x 4.43 and NO3-N = NO3- x 0.226.
Summary:
Monitoring nitrate levels in forage is crucial to prevent fatal poisoning and protect cattle producers’ livelihoods and animals’ well-being. It is essential to distinguish between NO3- (Nitrate) and NO3-N (nitrate-nitrogen) levels to make informed decisions. Laboratory reporting methods vary, with some measuring nitrate ion concentration (NO3-) and others focusing on nitrogen within the nitrate ion (NO3-N). Toxicity thresholds are crucial for ensuring forage safety and livestock health. Nitrate levels become concerning at 9,000-10,000 ppm, while nitrate nitrogen (NO3-N) poses a danger at 2,000-2,300 ppm. Recognizing these thresholds helps avoid toxicity risks and ensures livestock feed safety. Excess forage nitrates can indicate environmental issues like nutrient runoff, affecting water bodies. Understanding nitrate toxicity is crucial for agriculture and ecological conservation. Mastering nitrate conversion formulas is essential for accurately interpreting forage test results and determining feed safety. Key tips for producers and nutritionists include identifying the metric used, maintaining consistent communication, using conversion formulas, double-checking thresholds, keeping records, and consulting experts when in doubt.