Manure gases kill in MINUTES. Discover life-saving strategies every dairy producer needs NOW before emptying lagoons this spring.
EXECUTIVE SUMMARY: Manure storage systems pose lethal gas risks – methane explosions, hydrogen sulfide asphyxiation, CO₂ suffocation, and ammonia burns – particularly during spring agitation. Deadly hydrogen sulfide concentrations spike 1000+ ppm with gypsum bedding use, requiring mandatory gas monitors and textured lagoon escapes. Comprehensive safety demands annual OSHA-aligned training, 4-gas detectors, rescue equipment staging, and strict “buddy system” enforcement. Penn State research shows 60% of fatalities involve untrained rescuers, emphasizing non-entry rescue protocols. Producers must implement a 10-point safety checklist including perimeter fencing, emergency drills, and PPE compliance to prevent tragedies.
KEY TAKEAWAYS
- Hydrogen sulfide from gypsum bedding reaches instantly lethal 1000+ ppm during agitation
- 4-minute rescue window requires pre-staged poles/ropes – no heroics
- Textured liner strips cut HDPE lagoon drowning risks by 40%
- Daily gas monitor calibration prevents false security in oxygen-deficient zones
- Bilingual safety signage critical for non-English speaking crews
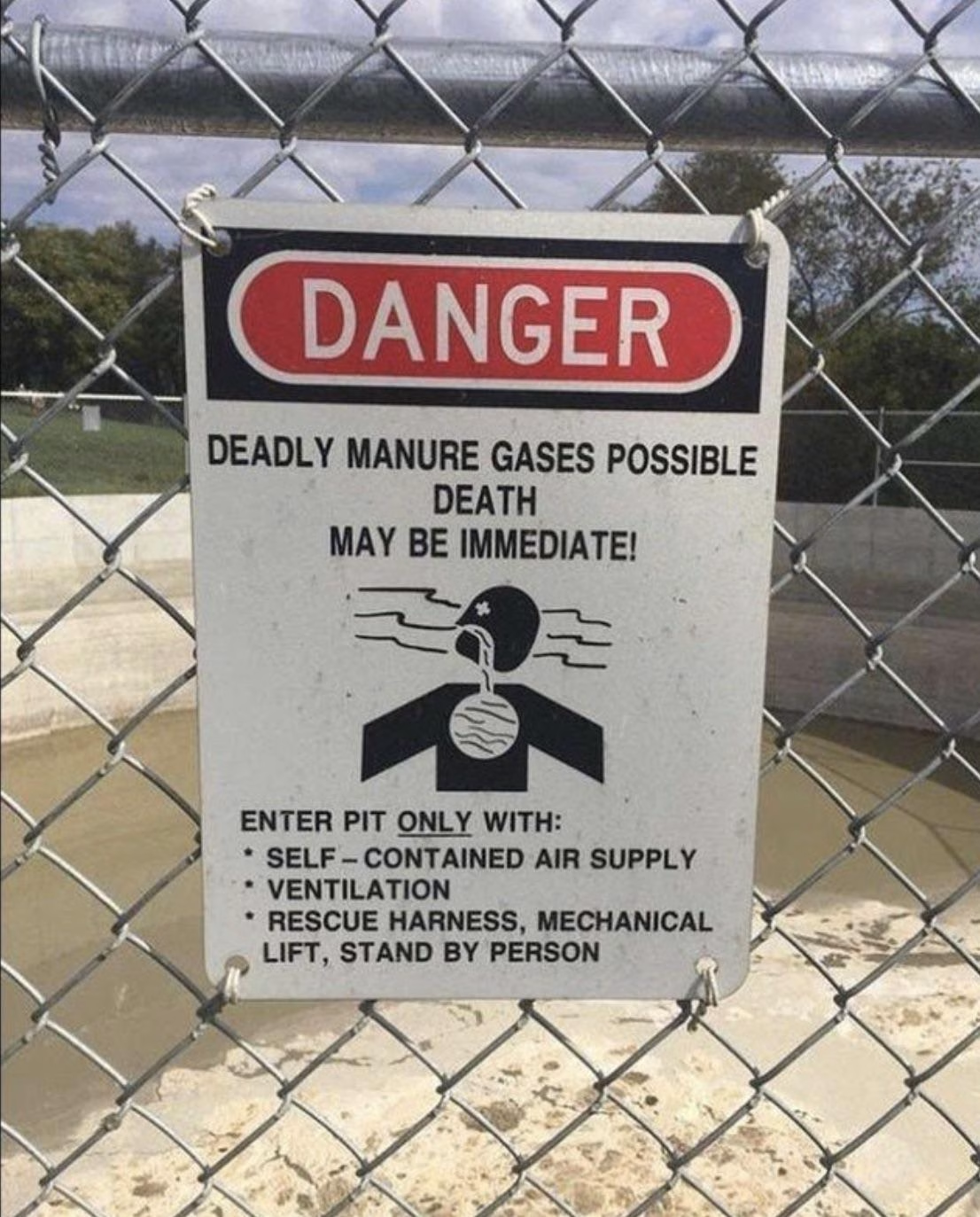
As spring manure application season kicks into high gear, dairy producers across the globe are emptying storage facilities and applying nutrient-rich manure to their cropland. But beneath the surface of this routine agricultural practice lurks a deadly threat that claims farmers’ lives each year. The gases generated in manure storage systems can kill within minutes, creating an invisible danger zone around lagoons and pits. Understanding these risks and implementing robust safety protocols isn’t just good business—it’s a matter of life and death for you and your farm team.
THE INVISIBLE KILLERS: UNDERSTANDING MANURE GAS HAZARDS
Every dairy producer must recognize that manure storage facilities produce a lethal cocktail of gases during decomposition. These aren’t just smelly nuisances—they’re potential killers hiding in plain sight.
COMPARATIVE GAS HAZARDS IN MANURE STORAGE
Gas | Flammable Range | Lethal Concentration | Detection Method | Primary Health Effects |
Methane (CH₄) | 5-15% in air | Oxygen displacement | Gas monitors only | Asphyxiation, explosions |
Hydrogen Sulfide (H₂S) | N/A | 600 ppm | Rotten egg smell 10% concentration | Gas monitors only |
Ammonia (NH₃) | N/A | 300 ppm | Pungent odor | Lung damage, eye irritation |
The primary gases of concern include methane, hydrogen sulfide, carbon dioxide, and ammonia, each carrying its distinct hazard profile. Methane, though odorless, poses a critical explosion risk when concentrations reach between 5% and 15% in air, potentially causing asphyxiation by displacing oxygen. This risk increases dramatically during agitation or when disturbing foam forms on manure surfaces.
HYDROGEN SULFIDE: AGRICULTURE’S SILENT KILLER
“Hydrogen sulfide is the leading cause of instantaneous death in agriculture. At 700 ppm, it can kill before you complete two breaths. Never trust your nose – use monitors religiously.”
OSHA Confined Space Safety Guidelines
Hydrogen sulfide deserves special attention as the most lethal gas in the manure storage environment. This colorless gas smells like rotten eggs at low concentrations but quickly deadens your sense of smell at higher levels, eliminating that crucial warning sign.
HYDROGEN SULFIDE EXPOSURE RISKS
Concentration | Effect Timeline | Health Impact |
10 ppm | Immediate | Eye irritation |
50-100 ppm | 1-hour exposure | Olfactory paralysis, nausea |
200 ppm | 3-5 breaths | Loss of smell, pulmonary edema |
500-700 ppm | 1-2 breaths | Immediate unconsciousness, death |
1000+ ppm | Instantaneous | “Knockdown” effect, rapid death |
At high concentrations, hydrogen sulfide paralyzes the respiratory system within minutes, leading to rapid death. Its weight makes it insidious, accumulating in low-lying areas around storage facilities.
Carbon dioxide, while not inherently toxic, creates danger through oxygen displacement. This odorless, colorless gas is virtually undetectable without specialized monitoring equipment and settles in low spots, creating oxygen-depleted zones that can cause headaches, dizziness, and, ultimately, asphyxiation.
Ammonia rounds out this hazardous quartet with its sharp, pungent odor that irritates the eyes and respiratory systems. While its strong smell typically provides a warning, high concentrations can cause severe lung damage or even death with prolonged exposure.
REAL-WORLD DANGER: WHY DEATHS STILL OCCUR
Despite widespread knowledge about these hazards, deaths and serious accidents continue to plague the dairy industry. Many producers understand the risks of confined manure handling systems but take unwarranted chances during routine operations. The most common contributing factors include:
- Inadequate employee training on specific hazards
- Missing or insufficient hazard signage
- Lack of appropriate safety equipment
- Communication barriers with non-English speaking workers
- Inability to provide clear location directions during emergencies
These seemingly simple oversights create the perfect conditions for tragedy when workers approach manure storage facilities unprepared. In 2018, multiple worker deaths occurred in manure pits, including Alberto Navarro Munoz, who drowned after his tractor tipped into a manure pit in Idaho. Another worker died attempting to rescue him—a tragically common occurrence in manure-related accidents.
BUILDING YOUR LIFE-SAVING TRAINING PROGRAM
Comprehensive safety training represents your first and most crucial defense against manure storage accidents. Every person who might work near these facilities needs thorough, regular education on the dangers they face.
ESTABLISHING A TRAINING REGIMEN
Your safety program should begin with new employee onboarding and continue with annual refresher training for everyone who works with manure handling and storage. The training schedule and documentation requirements are non-negotiable elements of a professional dairy operation:
- Provide comprehensive initial training for all new hires
- Conduct annual refresher courses for all employees
- Maintain thorough records of all training sessions
- Ensure materials are available in workers’ native languages
- Test comprehension through hands-on demonstrations
“Annual training isn’t a suggestion – it’s the difference between life and death. We’ve investigated 14 manure-related fatalities since 2020. Zero victims had current gas monitor training.”
USDA Manure Safety Report
CRUCIAL TRAINING TOPICS
Practical training must cover several essential areas to prepare workers for safe operations around manure storage facilities.
Gas detection represents a foundational skill for anyone working near manure storage. Workers must know how to accurately test for dangerous gas levels using portable multi-gas monitors to detect oxygen levels, hydrogen sulfide, methane, and other hazardous gases. This training should include proper calibration and maintenance procedures to ensure equipment reliability when lives depend on it.
Emergency procedures training should detail specific protocols for confined spaces, including pre-entry checks and safety measures. Workers must understand the critical importance of never entering a confined space without ensuring adequate ventilation and verifying safe air quality through testing. Training on rescue techniques—especially non-entry rescues that prevent additional casualties—could mean the difference between life and death in an emergency.
Personal protective equipment (PPE) selection, proper use, and maintenance are vital components of comprehensive safety training. Workers need instruction on the specific PPE recommended for manure handling, including:
ESSENTIAL PPE FOR MANURE HANDLING
Equipment | Protection Provided | Certification Standard | Inspection Frequency |
Multi-gas monitor | 4-gas detection | ATEX/IECEx | Daily calibration |
Full-face respirator | H₂S filtration | NIOSH P100 | Pre-use seal check |
Floatation suit | Buoyancy in lagoons | ISO 12402-5 | Monthly integrity |
Anti-static harness | Fall protection | ANSI Z359.1 | Weekly inspection |
Chemical-resistant gloves | Skin protection | EN 374 | Before each use |
RECOGNIZING SPECIFIC HAZARDS IN YOUR MANURE STORAGE SYSTEM
Different manure storage designs present unique hazards that require specific safety approaches. Understanding these design-specific risks is crucial for developing targeted safety protocols.
CLAY-LINED LAGOON HAZARDS
Clay-lined lagoons, standard in many dairy operations, present several distinct safety challenges:
- Earthen edges can appear deceptively solid while being prone to collapse
- Surface crusts form that look like stable walking surfaces but may not support a person’s weight
- Hazardous gases accumulate above the manure surface, especially during and after agitation
- Compromised clay liners may allow effluent to contaminate groundwater
HDPE-LINED LAGOON RISKS
Many modern facilities utilize HDPE (high-density polyethylene) liners, which present a different risk profile:
- The smooth HDPE surface becomes highly slippery when wet, dramatically increasing fall risks
- Damaged liners can create leaks, leading to environmental contamination
- Gas accumulation risks remain similar to clay-lined systems
Understanding these specific hazards allows you to implement targeted safety measures appropriate for your facility’s construction.
ENGINEERING SAFETY INTO YOUR MANURE STORAGE SYSTEMS
Physical safety features represent a critical layer of protection that works even when human vigilance fails. Smart engineering controls dramatically reduce risk with relatively modest investments.
ESSENTIAL PHYSICAL SAFETY FEATURES
For HDPE-lined lagoons, installing a textured liner section provides a crucial escape route, allowing individuals who fall into the lagoon to climb out more quickly. This textured surface offers better traction than smooth HDPE, especially when wet.
Perimeter fencing represents a fundamental safety measure for all manure lagoons. This barrier keeps livestock and unauthorized personnel—especially children—away from dangerous edges. Fences should stand at least four feet high with secure, adequately latched and locked gates. Maintaining clear areas around fencing ensures visibility and prevents easy bypass of this critical barrier.
Life-saving devices must be readily accessible near all manure lagoons. Essential equipment includes:
- Life preservers or ring buoys with attached ropes
- Throw ropes for distance rescues
- Rescue poles or reaching poles
- Safety harnesses with lifelines and secure anchor points
Regular inspection and maintenance of this equipment ensures it will function adequately during emergencies when seconds count.
COMMUNICATION: YOUR FIRST LINE OF DEFENSE
Clear and consistent communication represents a cornerstone of any effective safety program around manure storage facilities.
SAFETY SIGNAGE AND EMERGENCY INFORMATION
Warning signs must be prominently displayed and maintained around all manure storage areas. These signs should indicate specific hazards, including:
- Drowning risks
- Presence of deadly gases
- Potential for unstable surfaces like manure crusts
For operations employing non-English speakers, bilingual signage ensures everyone understands the warnings.
Emergency contact information must be posted near the lagoon and at all telephone locations. This information should include:
- 911 emergency number
- Local fire department or rescue squad contacts
- Facility management personnel phone numbers
- Precise location details to aid emergency responders
- Accessible emergency action plans detailing response procedures
IMPLEMENTING LIFE-SAVING WORK PRACTICES
The final layer of protection comes from establishing and enforcing strict work protocols around manure storage facilities.
MANURE EMERGENCY RESPONSE PROTOCOLS
Time Since Incident | Required Actions | Equipment Needed |
0-2 minutes | Activate emergency alarm | Air horn/alert system |
2-5 minutes | Deploy non-entry rescue tools | Rescue pole/throw rope |
5-10 minutes | Ventilate area | Explosion-proof fan |
10-15 minutes | Call 911 with location details | Posted emergency info |
15+ minutes | Await trained responders | SCBA equipment |
“In manure emergencies, you have 4 minutes max. After that, it’s body recovery – not rescue. Drill like your life depends on it… because it does.”
National Fire Protection Association Farm Response Manual
ESSENTIAL PRE-WORK SAFETY PROTOCOLS
Access restrictions form the foundation of safe operations. Limit manure storage access strictly to authorized, trained personnel through perimeter fencing, locked gates, and clear warning signs. Keep unnecessary bystanders—especially children—away from lagoons during hazardous operations like agitation or pumping.
The buddy system saves lives. Never allow anyone to work alone around a manure lagoon. Always have at least one other trained person present who can immediately assist and summon help in emergencies.
A comprehensive emergency action plan must be developed, documented, and communicated to all employees working near manure lagoons. This plan should outline specific procedures for gas exposure incidents, falls into the lagoon, and manure spills. Regular emergency drills ensure all personnel understand their roles during crises.
SPECIAL HAZARD: THE GYPSUM BEDDING CONNECTION
Recent research has identified a significant but often overlooked danger: gypsum bedding dramatically increases hydrogen sulfide production in manure storage systems. When gypsum (calcium sulfate) enters manure storage, the anaerobic environment converts the sulfate to hydrogen sulfide gas at much higher levels than normal manure.
“Our monitoring showed H₂S levels exceeding 1,000 ppm within 20 minutes of agitation when using gypsum bedding. That’s instant death territory. Producers using gypsum need military-grade vigilance.”
2024 Penn State Dairy Science Study
Monitoring conducted by Penn State University found that farms using gypsum bedding experienced dangerous hydrogen sulfide levels during manure agitation, while farms without gypsum had almost no detectable hydrogen sulfide. The highest gas concentrations occurred during the first hour after mixing began.
If your operation uses gypsum bedding, you must implement additional safety measures:
- Purchase portable hydrogen sulfide monitors (available for under $300) for all workers
- Establish longer waiting periods after agitation begins before allowing workers near storage areas
- Consider alternative bedding materials if your manure storage system cannot be adequately ventilated
- Implement more frequent gas monitoring during all manure-handling activities
UNDERSTANDING THE DEADLY GASES
To better understand the specific threats you’re dealing with, here’s a breakdown of the four primary gases found in manure storage systems:
METHANE (CH₄)
- Properties: Odorless, colorless, lighter than air (accumulates at the top of enclosed spaces)
- Concentration danger: Flammable/explosive at 5-15% concentration in air
- Health effects: Primarily an asphyxiant that displaces oxygen
- Warning signs: None—cannot be detected without monitoring equipment
- Unique risks: Can become trapped in foam on manure surface, creating explosion hazard when disturbed
HYDROGEN SULFIDE (H₂S)
- Properties: Colorless, heavier than air (settles in low areas)
- Odor: Rotten egg smell at low concentrations but paralyzes sense of smell at higher levels
- Concentration danger: Rapidly fatal at 500-700 ppm
- Health effects: Low concentrations cause eye irritation, dizziness, and nausea; high concentrations cause respiratory paralysis and death within seconds
- Warning signs: Initial rotten egg odor that disappears as concentration increases
- Unique risks: Dramatically increased production when gypsum bedding is used
CARBON DIOXIDE (CO₂)
- Properties: Odorless, colorless, heavier than air (settles in low areas)
- Concentration danger: Displaces oxygen, leading to asphyxiation
- Health effects: Causes labored breathing, drowsiness, headaches, and eventually unconsciousness
- Warning signs: None—cannot be detected without monitoring equipment
- Unique risks: Produced both by manure decomposition and livestock respiration
AMMONIA (NH₃)
- Properties: Colorless, lighter than air
- Odor: Sharp, pungent smell that irritates eyes and respiratory system
- Health effects: Irritates eyes, nose, throat, and lungs; high concentrations can cause severe lung damage or death
- Warning signs: A strong, irritating odor provides a natural warning
- Unique risks: Higher concentrations in poultry manure
Remember that during agitation or pumping, these gases are released rapidly from the manure in concentrations far higher than during regular storage. This is why most fatalities occur during manure-handling operations rather than routine farm activities.
TAKING ACTION: YOUR MANURE SAFETY CHECKLIST
As spring application season continues, now is the perfect time to review and strengthen your manure storage safety program. Implementing these practical measures immediately can prevent tragedy in your operation:
- Install textured liners in HDPE-lined lagoons to create escape routes
- Establish perimeter fencing with locked access points
- Position life-saving devices at strategic locations around storage areas
- Implement a portable gas monitoring program with daily bump tests
- Display clear warning signage and emergency contact information
- Develop and document emergency action plans
- Establish a comprehensive training program
- Enforce the buddy system for all manure storage work
- Provide appropriate PPE and ensure proper use
- Conduct regular safety drills and equipment inspections
“Your lagoon isn’t ‘just manure’ – it’s a chemical weapon. Manage it with the same respect you’d give a live grenade.”
Dr. Michael Murphy, Agricultural Safety Specialist
Modern manure management systems’ increasing scale and complexity have amplified safety risks in today’s dairy operations. By understanding the specific hazards, implementing robust safety features, and establishing clear protocols, you create layers of protection that can prevent the unthinkable from happening on your farm. Remember—these aren’t just good practices; they’re life-saving necessities that protect your most valuable asset: the people who make your operation successful.
Learn more:
- What Reed Hostetler’s Tragic Loss Can Teach Every Dairy Farm
This article explores the devastating consequences of neglecting manure pit safety and offers actionable protocols to prevent similar tragedies. - Riverview Dairy’s Massive Expansion: A Death Knell for Small Dairy Farms
Learn how large-scale dairies are turning manure into renewable energy, while addressing methane hazards and environmental concerns. - Optimizing Dairy Manure Application Rates for Enhanced Field Productivity
Discover practical tips for safe and efficient manure storage, handling, and application to maximize farm productivity and minimize risks.
Join the Revolution!
Join over 30,000 successful dairy professionals who rely on Bullvine Daily for their competitive edge. Delivered directly to your inbox each week, our exclusive industry insights help you make smarter decisions while saving precious hours every week. Never miss critical updates on milk production trends, breakthrough technologies, and profit-boosting strategies that top producers are already implementing. Subscribe now to transform your dairy operation’s efficiency and profitability—your future success is just one click away.